

Device recognition & telematics

The TracLink system includes many useful functions that will make your work easier and make it easier to understand. It is the ideal solution to keep an eye on your fleet at all times.
Locating
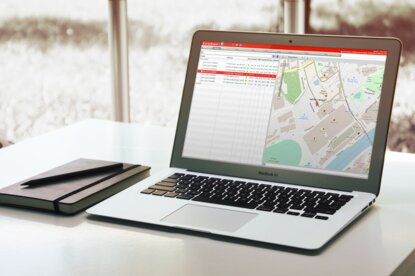
Vehicles equipped with the telematics functions of the TracLink can be located in real time. In addition the current driving speed, a digital logbook, digital mission documentation, performance reports and all vehicle information (engine speed, hydraulic control units, AdBlue, tank level, current fuel consumption, PTO status, outside temperature, active fault codes, service info, operating hours and mileage ) can be accessed.
It is possible to integrate other vehicle manufacturers in the TracLink system.
As a result the user has an perfect overview on his vehicle fleet.
Statistics
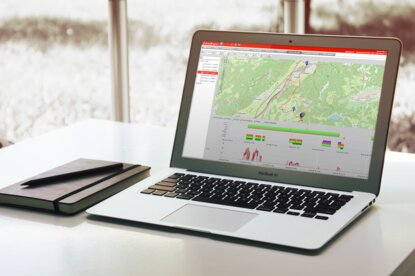
Due to the exact documentation in the TracLink portal, a variety of statistics on the used vehicles and equipment can be created. Including the total operating hours and -kilometers as well as the average fuel-, AdBlue- or grit consumption.
Alerts
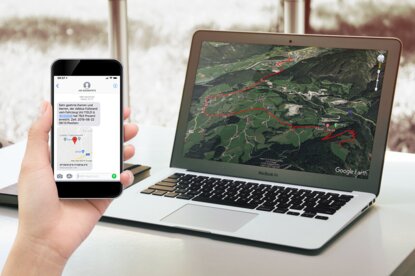
The TracLink system automatically displays active error codes as soon as problems crop up. In addition, warnings can be specially configured and optionally sent by email or SMS. In this way various actions such as reached customers, maximum speed or information on coming service can be created.
Analysis & Documentation

The TracLink portal provides you a comprehensive surface- and customer administration. Use a few clicks on the map to define mission areas for your city or other customers. You can focus on your work and TracLink evaluates the electronic logbook for you afterwards. As an example: You can easily create monthly billing statements for winter service missions - including all of the important informations about the working time, the ploughed area and the amount of salt. Scattering logs can be made on your own in a few simple steps and printed out at any time.
Device detection
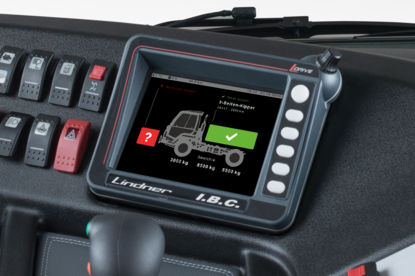
In order to connect devices from various manufacturers to the TracLink system, the attachment is provided with a TracLink chip. This enables data transmission between the device and the vehicle or TracLink. The driver approaches the device, this is automatically recognized by the system and a connection and operating help is displayed on the IBC (Intelligent Board Computer).
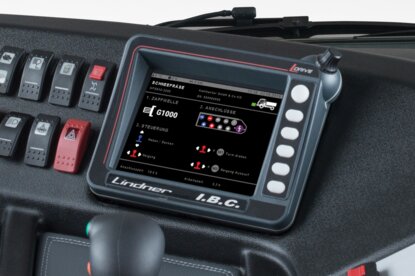
The driver will see the PTO gear, the necessary hydraulic couplings and the individual control of the unit.
Integration of spreader control
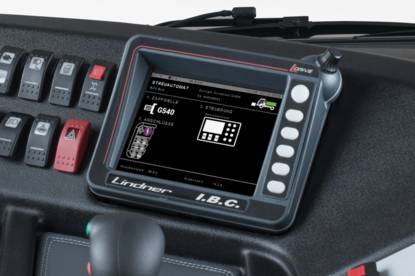
The integration of many established operator terminals of various spreader manufacturers in the TracLink system is possible. As a consequence even complex sensors on the device for example spread rate control or road temperature detection can be integrated. Data transmission according to DIN-EN-15430 Data interface in the vehicle.
Traffic Safety Check
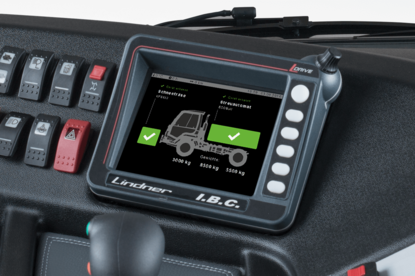
When all devices and the vehicle are connected to each other via the TracLink system, the driver is informed that the vehicle is in a safe condition and that the prescribed equipment or protective cover is present.
Operating hours
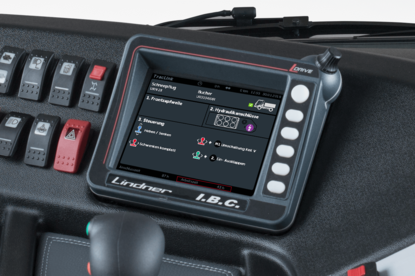
With the TracLink system operating hours of the attachments can be recorded in detail. This makes it easy and quick to see the working time of the attachment. As a result maintenance or service of the attechments are possible timely . When the attachment is rented, the time used can be very easily calculated by the detailed recording of the working time.
Weight Detection
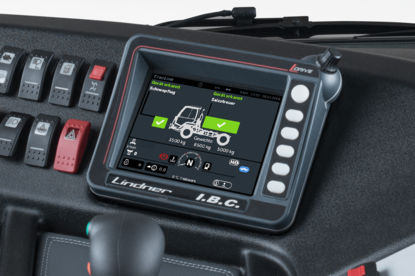
By connecting individual devices with the TracLink system, it is possible to calculate and display the exact axle load. This total weight calculation also includes the connected equipment. As a result the actual filling weight of e.g. manure or road salt can be included into the measurement.
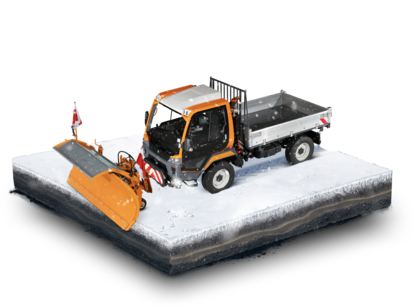